When does a gimmick end up as a useful, saleable product? When designers and engineers see that it will solve a problem! That is just what happened when Ceramco made some nuts and bolts out of ceramic material (alumina) for promotional purposes. Seeing these nuts and bolts on display at an industry trade show, people started asking about their properties and availability, and then started using them.
Since then, the gimmick has become a 3-catalog product line with sales around the world. Standard sizes range from 1/4-20 to 0-80, up to 3 inches long. Many head configurations are currently available – and essentially any head configuration can be made – but the hex head is standard.
The specific applications for these alumina nuts, bolts, and washers are varied, but some common themes recur. Typically, these ceramic nuts and bolts are used for non-stress fastening in moderate and elevated temperature environments. In most cases, these applications relate to electronic equipment and their assembly, eliminating metals from consideration due to their electrical conductivity.
Although polymers such as nylon, Delrin® and Teflon® come to mind for such fasteners, the alumina ceramic parts are often favored in applications where the performance of such polymers is compromised over time due to temperature and cycling aspects. Even in moderate temperatures of 200 – 300°F, these polymers will soften, deform, oxidize and become brittle over time, resulting in failure at some point. Temperature cycling can exacerbate these problems, as can other environmental factors.
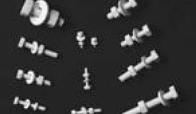
Injection-molded ceramic fasteners from Ceramco, Center Conway, NH, come in handy for non-stress applications in electrical equipment, replacing fasteners made of plastic. They are electrically insulating and work well in corrosive or high-temperature environments such as metal plating and industrial kilns.
Although the temperatures of these applications are actually far below what alumina can withstand, these ceramic fasteners address the problems of metal and plastic alternatives – alleviating concerns over fastener failure. Since such failure can result in the dislodging of internal components, causing equipment interruption and/or shut-down, the peace of mind provided by the alumina fasteners is important.
Other moderate temperature applications for the alumina nuts and bolts include their use for fastening purposes in highly corrosive environments, like metal plating operations, since they are unaffected by any acids except for hydrofluoric.
In more severe environments, such as those found in high temperature industrial kilns and heat treating furnaces, where temperatures are typically from 900°C to 1600°C, these nuts and bolts are extremely useful. They are used to fasten the furnace insulation, to hold fixtures together inside the furnace, and in some instances to bolt-hold the heating elements themselves.
The drawback in using ceramic fasteners is that they are brittle and will break if subjected to hammer-like impact or excessive torque. However, if they are installed and used properly they will perform almost indefinitely.
The benefits of ceramic nuts and bolts for fastening applications ultimately translate into improvements in productivity – via decreased downtime and decreased equipment maintenance. An increase in the useful life of the equipment is also possible.
“Our components must function in ultra high vacuum and high voltage environments. The ceramic screws that we use circumvent problems associated with metal screws, such as offgassing and arcing, while providing good holding power and strength.”
– Jay Ray, Vice President, Detector Technology