Certain environments are particularly troublesome when it comes to choosing materials of construction. Think about processes – whether at ambient or elevated temperatures – where chemicals, pollutants, oxidation and ozone are an everyday occurrence. Add to this the need for “stripping” by way of gas diffusion processes and you have a real challenge on your hands. And don’t forget the need for process efficiency.
Refractron saw this challenge as an opportunity for its advanced porous ceramics. These ceramics are known for their durability, chemical corrosion resistance, permeability and application-specific pore size distribution. In addition, they are stable to over 800°C. Hence, they are able to survive in severe environments like those above.
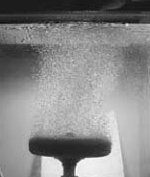
Porous ceramic replaces plastic, sintered metal, and exotic alloys in gas diffusers for corrosive, abrasive, and high-temperature applications. The Solidome™ gas diffuser made by Refractron Technologies, Newark, NY, is used in the aeration and oxidation of various liquids. A ceramic-membrane coating process produces diffusers with pore sizes from 0.1 to 30 µm.
But what about process efficiency? Gas diffusion processes are used for aeration and oxidation of various liquids. That said, the ideal gas diffusion system should generate a high volume of ultra small gas bubbles for maximum efficiency.
Traditional gas diffusion processes may use components such as injectors made of plastic. However, they can wear prematurely and do not deliver the desired efficiency. Monolithic structure ceramics, because of their desirable physical properties, may also be used. Unfortunately they offer no control over mean bubble size or bubble distribution, resulting in poor performance and efficiency. Alternatively, porous sintered (powdered) metal diffusers can be considered – since they have some characteristics similar to monolithic ceramic diffusers – but the metal will corrode in severe chemical environments.
Working in conjunction with several municipalities, and leveraging its porous ceramic technologies, Refractron addressed this challenge. The net result is the company’s development of what is now known as the SolidomeTM Gas Diffuser. This patented technology utilizes a porous ceramic that is designed to survive in corrosive environments and which improves gas transfer efficiency by providing ultra fine gas bubbles in the gas diffusion process. The design, which incorporates a ceramic membrane coating, produces fine, evenly distributed gas bubbles with minimal differential pressure. The benefits of this design include high transfer efficiencies, low pressure drops and very narrow bubble size distribution.
The net result on the diffusion process is that this ceramic solution generates ultra high gas mass transfer efficiencies in high concentration/low flow applications where energy and operating costs are an issue. Originally designed for high concentration ozone systems – where it can survive the corrosive ozone environment such as in water treatment applications – the Solidome is also useful in severe environments such as those associated with the oxidation of pollutants, chemical stripping operations which use gasses such as CO2, N2, O2, etc.), biological reactor processes, and any number of industrial applications where diffusion of a gas into a liquid is required.