How do you get a component with fine-sized pores that is resistant to molten Aluminum and won’t plug up?
This is just the problem that plagues those who manufacture aluminum parts from molten aluminum, such as automotive wheel and structural component manufacturers. Part of the manufacturing process involves a degassing step which removes unwanted hydrogen from the molten aluminum. The hydrogen is present in a dissolved state as a result of the metal’s exposure to moisture, hydrocarbons and other process elements. Hydrogen is removed from the aluminum in order to provide a higher quality aluminum product. If not, the hydrogen can get trapped in the metal during the solidification process, leading to porous aluminum parts with inferior properties.
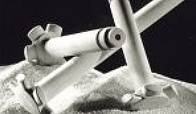
This composite-ceramic degasser removes hydrogen gas from molten aluminum. A combination of freeze molding and injection molding lets Blasch Precision Ceramics, Albany NY, make a permeable ceramic from a silicon carbide/alumina composite.
The “cleaning” process is accomplished by bubbling gas (i.e. nitrogen or argon) through the molten aluminum bath. The hydrogen attaches itself to the gas bubbles and is removed. The bubbling also helps to float undesirable aluminum oxide (resulting from molten aluminum’s exposure to air) to the surface of the molten bath for removal – again to prevent entrapment in the cast part.
In the more prevalent “dynamic” systems, the gas is typically introduced via a rotary degassing unit which incorporates a shaft/head component that delivers the gas – via bubbling – into the molten aluminum. For maximum degassing efficiency, a large quantity of very small gas bubbles is required. Productivity calls for a long service life from the degassing components.
In the past, graphite was used for the shaft/head component. It is a relatively strong material and easily machined. The head portion required the presence of small holes – which were machined into the part – for gas delivery. The problem with graphite, however, is that it oxidizes at molten aluminum temperatures (1400°F) resulting in degradation, shortened productive life and the need for replacement.
The more stressful dynamic systems – where shaft rotations can range from 200 to 400 rpms – are especially troublesome regarding shaft warpage and/or breakage. In addition, although many very fine holes are desirable for degassing efficiency (as noted above) the machined holes in the graphite are comparatively large.
Since these machined gas-exit holes on the head can plug during solidification, the graphite system has limitations – both by design and by operation over time – in terms of degassing efficiency and aluminum quality. All these problems translate into increased operating costs for the aluminum part manufacturer.
Enter another ceramic solution. Here, Blasch utilized its unique ceramic technology for injection molding and freeze molding, along with a novel approach to the material itself, to arrive at a component which solves the problems above. The material is a composite of silicon carbide and alumina which is not oxidized by aluminum nor by the treatment gas. It is combined with a non-wetting additive to minimize wetting and/or penetration by the aluminum. In addition, since the ceramic manufacturing process provides a ceramic component with “built-in” permeability where the pores are at or below 5 microns in size, they resist metal penetration, while allowing gas flow.
The Blasch process also enables different levels of porosity to be designed into a single component. In this case the shaft has lower permeability so it conveys the gas to the head, and the head has very high permeability to provide the high quantity of small gas bubbles that is desirable for degassing efficiency. The release of the gas into the melt is readily controlled by adjusting the gas pressure.
All those features provide benefits – namely a component with good mechanical strength, resistance to wetting by aluminum, oxidation resistance and therefore erosion resistance, enhanced durability and lifespan, improved degassing efficiency due to the presence of many fine pores, and minimized impact from plugging because of the absence of macro-holes.
The net result is a component which addresses the deficiencies and improves performance of existing degassing systems, resulting in increased utilization of existing capital equipment, reduced operating costs and higher quality aluminum parts.
Patents are pending on various rotor designs and materials.