Continuous processes always demand “extra” from the system’s components. Since the key is to run “continuously”, anything that can be done to reduce downtime and enhance productivity contributes to the bottom line. But what if your continuous process involves the need to assure a smooth even “flow” for hundreds of tons of molten steel through a ½” orifice, as is the case with the continuous casting of steel billets? Enter ceramics.
Ceramics have indeed been used for many years for what are called tundish nozzles. These nozzles direct the flow and maintain the supply of molten steel to the molds in the continuous casting of steel. The nozzles are mounted on the bottom of the tundish – a huge vat (endearingly called the bathtub by some) which receives 3 – 25 tons of molten steel at a time from the furnace via ladles.
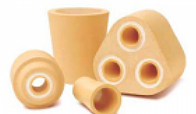
A tundish nozzle for manufacturing steel, developed by Zircoa, Solon, OH, has a fine-grained zirconia liner inside a more conventional coarse-grained nozzle. The insert has higher density and strength, and lower porosity than the surrounding material. This improves dimensional stability and resistance to erosion and corrosion.
A smooth, controlled even flow of the molten steel through the nozzle and into the billet helps to assure homogeneity of the steel and therefore higher quality billets and downstream products, such as rolled wire and reinforcement bar (rebar). The more turbulent the flow – and the more the process is stopped and started – the lower the steel’s homogeneity, the lower the quality, and the higher the operational costs due to scrap.
Since molten steel has a viscosity similar to that of water, the nozzle plays a critical role in maintaining both a constant rate-of-flow and a steady, smooth flow of the molten steel into the molds.
If the flow rate is not constant the molds may be under or over filled, causing process control headaches and generation of scrap. At the nozzle’s contact surface, as little as “thousandths of an inch” of erosion (from the flow of steel over time) or corrosion (from the chemical constituents in the steel) can have the effect of increasing the size of the orifice and therefore changing the flow rate.
The flow quality is altered by erosion or corrosion (see above) and/or cracks in the nozzle. The cracks can result from thermal shock; the nozzle can be exposed to rapid temperature changes – from ambient to 2800°F – within minutes. Whether via erosion, corrosion or thermal shock, the resultant surface imperfections translate into ragged or misdirected flows to the mold.
Coarse grain zirconia, the traditional material of choice, has properties important to this application: erosion resistance, corrosion resistance, temperature stability, and resistance to thermal shock. The resultant tundish nozzles provide a reasonable solution to the need for a steady and smooth flow of molten steel in the continuous casting operation, although the severity of the application does require that the tundish nozzles be monitored and replaced as needed.
For those continuous casting companies wanting to advance to the next level of performance and productivity a recent development has made that possible.
Zircoa, a supplier of traditional coarse grain zirconia tundish nozzles to the steel casting community, is also involved in advanced high performance ceramics. By combining their two capabilities, a novel “composite” nozzle is now available which addresses the need for improved performance.
The “composite” nozzle (called the DenZborTM nozzle) consists of a thin-wall impervious high performance fine grain zirconia ceramic “liner” (insert) supported by a conventional coarse grain zirconia nozzle “holder” (body). The insert, by being made from fine grain material, has higher density, lower porosity and higher strength than the coarse grain equivalent, resulting in enhanced resistance to erosion and corrosion. It holds dimension well, enabling improvements in molten steel flow control and flow quality and therefore billet quality.
The body (made of traditional coarse grain zirconia) houses the insert and provides the appropriate “fit” with the nozzle block. It also enables effective utilization of the high performance insert material and its superior properties where it is critically important – in direct contact with the molten steel – providing enhanced performance only where it is needed.
This cost-effective combination of ceramic materials provides the continuous caster of steel numerous benefits, all of which contribute to increased productivity and decreased costs. The composite nozzle lasts 3 times longer than the traditional nozzle, resulting in fewer interruptions to the process. This translates into increased productivity and decreased costs (less scrap).
An additional benefit from the reduction in nozzle replacements is that fewer tundish (bathtub) relines are necessary. Each reline can easily cost $10,000 in labor and materials, not to mention the cost associated with lost production. (In relining, the solidified remnant steel is chiseled out of the tundish and the necessary refractory materials are replaced; this is required every time a nozzle is replaced.)
Given the success of this composite nozzle, similar composite approaches are now being considered in other parts of the steel casting process.